Hot Rolled Steel Vs. Cold Rolled Steel
With the many different methods of processing steel and enhancing it for use, it can be difficult to decide which variety of steel is best for you. Accordingly, one of the most common quandaries that manufacturers encounter is whether hot rolled steel or cold rolled steel is the ideal choice for them. Both forms of rolled steel have their own unique qualities, which begs the question: which one is the best choice for you? Today, we’ll be comparing and contrasting the uses of hot rolled and cold rolled steel for people in all industries.
Hot Rolled Steel: Building the Essentials
Hot rolled steel is the go-to for manufacturers everywhere because of its cost efficiency and low level of internal stress. The majority of hot rolled steel’s transformation takes place during the intense heating process, in which the steel is rolled at temperatures of at least 1700°. During the heating process, the steel (which has attained temperatures above its recrystallization process), is formed into the desired shape before being left to cool.
The cooling process for hot rolled steel ensures two distinct qualities that contrast cold rolled steel:
- Miniscule internal stress due to the metal resettling and binding
- Variations in structure due to the steel resettling
Because of the reduced internal stress and the unpredictable variations in the steel’s structure, there are a variety of pros and cons to consider if you plan on using hot rolled steel:
- Pros: Cost-Effective; Easy Shaping; Malleable; Fast Turnaround
- Cons: Not suitable for precise shaping; prone to distortion
Given the above qualities of hot-rolled steel, it has long been the rolled steel of choice for agricultural equipment, construction material, and car parts.
Cold Rolled Steel: Precision and Consistency
On the opposite side of the same rolled-steel coin is the process of cold rolling.
Cold rolled steel isn’t “cold rolled” in that it’s exposed to freezing temperatures; it’s just left to cool at room temperature for an extended period of time. As a result, the steel is given more time to settle before compression, increasing its strength by up to 20%. The steel is then compressed at room temperature.
This process gives cold rolled steel two unique qualities that hot rolled steel doesn’t have:
- Better finish and more precise, controlled final shape.
- More labor-intensive processing that requires additional oversight.
These two traits make cold rolled steel highly sought after, but less common than hot rolled steel. If you’re considering using cold rolled steel, then you should keep the following pros and cons in mind:
- Pros: Stronger than Hot Rolled; Better Finish; Precise Design; Higher Tolerance
- Cons: More laborious to create; slower turnaround time
Because of its unique strengths and weaknesses, you’ll generally find cold rolled steel used for aerospace technology, home appliances, and mechanical components.
Ultimately, whether you choose hot or cold rolled steel is a decision you’ll have to make for your manufacturing. However, you don’t have to make it alone. For more information on whether hot or cold rolled steel is right for your manufacturing, contact our team at Atlas Steel for a consultation on our services today.
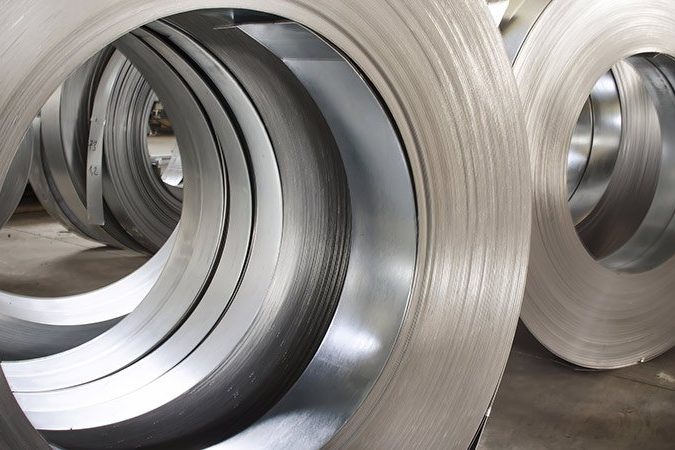